Purpose and content of this post
The goal of this post is to define supply chain management in the present world and in the context of building and/or choosing the right software systems and platforms to manage supply chains. As supply chain leaders and practitioners, our GRID team and I have worked and engaged with hundreds of companies as a part of initiatives to digitize their supply chains: traditionally, the description of supply chains was restricted to outbound operations and logistics management. Supply chains in the real world however are more complex and far wider/longer. Secondly, the modern supply chain has different needs, definitions, and scope. This piece will correspondingly get into the expectations of today’s supply chain manager and executive from their software systems such that they can effectively address the needs across the entire length of their supply chains. This blog will further serve as an instructional guide for decision makers and power users on what they should be looking for in their next-generation supply chain platforms.
For ease of typing and reading, the acronym SCM has been used in this post for Supply Chain Management.
Definition
Supply chain management historically was management of the flow of goods and services through assembly of raw materials, manufacturing, distribution of finished goods. The important edit to this definition is that supply chain management is the flow of goods, services, AND information. It is impossible to run and manage an efficient supply chain without having access to real time digital information in parallel to the flow of physical goods. The flow of goods is mostly and ideally single-directional barring exceptions with returns, corrections etc. The flow of information is across-participants and many-directional. For today’s supply chains, access to this digital information is more critical than managing the flow of goods. This is not to say that the monitoring of the flow of goods is not important. But measured as a percentage, companies should be investing more resources into the storage, access, and visualization of digital information since the long term impacts and implications on the health of a business of having/not having this information are far more significant.
History of SCM software and Scope of SCM software
Historically and even until recently the category of SCM was nonexistent. Companies always had SCM functions that needed digital help, but they turned to ERPs as the overarching solution to manage accounting, HR and some SCM operations. And since most established ERP systems were outbound-supply chain focused, the supply chain sections that got digital attention were mostly purchasing, inventory and distribution. These systems were also expensive, had years-long implementation timelines and were priced by user license – this complicated combination meant access was restricted to corporate users. Unfortunately, despite all the investment and effort, companies still had not achieved the goals of full digital visibility and connected supply chains.
To be able to build next generation connected supply chains, companies need to better define a comprehensive scope functions list across their supply chains and corresponding software solutions expectations.
Below are simplified scope descriptions across major consideration categories. These include,
Organized by supply chain function:
1. Product Design and Development
Ability to manage product design attributes, manage product collections and technical specifications, and track development workflows and owners.
2. Vendor profiles and compliance
Add vendors, maintain profiles, and manage compliance information, ratings, ongoing performance, and certifications
3. Costing
Product specifications’ data connected to cost templates that allow costing to be entered at granular level across bill of materials, shipping and other inputs making up finished product costs. Ability to visualize finished product costs at the aggregated level.
4. Price comparison, bid management
Invite vendors and sourcing participants to submit bids at preferred level of granularity and compare bids to make the best selection.
5. Purchasing
Create and issue purchase orders across products. Connect and add product, vendor, shipment, and freight data as relevant.
Here is a deeper read on PO functionality must-haves.
6. Invoicing and payments
Create, issue invoices, and pay vendors and other supply chain participants.
7. Inventory
Scan and track raw materials and finished product inventory in transit and by warehouse location.
Some more information on how data and reports from inventory systems can help action smart decisions for your business.
8. Shipments
Split and/or aggregate purchase orders across shipments.
9. Distribution and freight
Connect shipments to freight data across different legs including through the last mile and delivery to customer.
Organized by functionality required across all supply chain functions:
In addition to functionality across each supply chain function, solid SCM systems need to support certain mission critical cross-function features. This list is arguably more important than core operations’ functionality.
10. Collaboration and communication
Modern supply chains recognize the importance of empowering all participants – employees, 3rd party agents, vendors, suppliers, factories, 3PLs, warehouses and more – with a seat at the digital table. As users increase, the value realized from a software platform exponentially increases. It is not enough to just provide access to participation. Successful systems have intuitive design and simple interfaces that allows all participants to effortlessly collaborate with one another and across the length of the value chain.
11. Digital asset management
A huge quantity and variety of digital assets are created and referenced across product creation, manufacturing, and distribution. Digital asset management becomes table stakes functionality – ability to create and/or upload and integrate all file types, power to create different file templates, and to search and filter files based on the fields and content within each file.
12. Reporting, dashboards, and analytics
With all the data tracked and stored across the endless length of the supply chain, systems that provide the power to the user to extract intelligence from this data become irreplaceable. We want systems that give the user the ability to configure reports built on the strength of connected data sets. Diving a little deeper here, this is a big opportunity area for both software platforms as well as customers. There is vacuum to be filled and a need for a clever, simple architecture that houses and connects the disparate data sets across supply chains. Even simple reports that track basic operations like critical path management can provide “ah-ha” insights and drive exponential returns for the business.
13. Integrations
The above list is a lot, yes. Our Suuchi Inc team is of the belief that with master UI and UX and cleverly curated functionality, most modern SCM needs can be addressed with one platform. The modern company does not want a dozen systems clogging their supply chain tech stack. Having said that, some companies will want point solutions to go deeper into certain areas of the supply chain. Further, not all legacy systems can be sunset and will have to be made part of the solution. Standardized integrations with current systems become must-have when making decisions on the single supply chain platform. Since there is a long tail of legacy systems, not all these integration points however may have standardized plug-ins. It is essential to pick a supply chain software vendor that has a dedicated team for integrations and can be flexible to define solutions for atypical integrations.
Future-proofing your SCM software decision
The traditional ERP and legacy systems come attached with limitations. Any supply chain management solution implementation is intensive in terms of time and resource investment. The decision and execution must be done right for today and tomorrow. A few recommendations on 6 critical decision parameters that will help ensure you future proof your decision:
1. On prem versus cloud subscriptions
It is shocking how many companies still run their systems on premise and with perpetual license models. This model severely disables companies versus running on a combination of public (and/or private) clouds and getting the benefit of new functionality released in real time as a part of subscription software services. One of many advantages is flexible space for storing and processing huge amounts of data that are a natural outcome of running complex supply chains.
2. Connected data sets
With the huge amount and variety of data being collected across every function of the supply chain, having these data buckets connected and communicating with one another helps with minimizing overhead with manual re-entries and helps with avoiding errors. Connected data sets further create a strong foundation for the reporting and analytics application layer.
3. Single source of truth
Even if your company has many disparate systems sitting across the tech stack, ultimately it is critical to have one platform function as the single forum across all teams and functions and function as the supply chain’s single source of truth. Evaluating if the system in consideration can play the role of the single source of truth should be an important parameter in influencing the final decision.
4. Front end configuration
Even if two companies are identical in the industry they operate in, products they distribute and how they sell them, their supply chain workflows can still be different. From our experience at Suuchi Inc working with hundreds of companies and their supply chains, we’ve seen that no 2 workflows are exactly identical. Every company has needs for custom fields, templates, and workflows. Instead of making engineering requests requiring endless customization, transferring the power to the end user to configure their needs on the front end can be transformative. In the long term it increases stickiness with the system but also saves resource investment.
5. Easy to use UI and intuitive UX
To democratize access and allow all participants a seat at the digital table, the user interface and user flow should be easy and simple to allow use for different skills sets across participant segments. The SCM software vendor should show a real investment in their UI philosophy and their teams in charge of building out the front ends.
6. Pricing models and managing for optimized TCO (total cost of ownership)
The traditional model of pricing for software systems is by user. While this is not the worst thing, as a company scales in terms of internal and external users, the total cost of ownership can balloon out of control. It is wise to look for hybrid pricing systems where pricing is segmented by blocks of users versus per user and where there is an easier price point for the larger ocean of external users. Another model that is helpful as a combination price model is cost that increases with usage or as a percentage fee of transactions processed.
Expectations from SCM software and how to make a decision
Not all functionality needs to be available on day 1.
SCM software implementations are large projects, and the implementation process is as important as the pre-sales decision process on the system. Phasing the implementation of a software platform is a smart move to maximize value and adoption. Another approach is start with simpler functionality where the digital system may address the most important needs, and then to phase into a point solution addressing more complex needs. An example of this approach when evaluating digital needs taking one supply chain function is outlined here.
Here are a few other articles we have written on how to make an informed decision on your supply chain platform.
For more supply chain and supply chain management visit us at Suuchi Inc
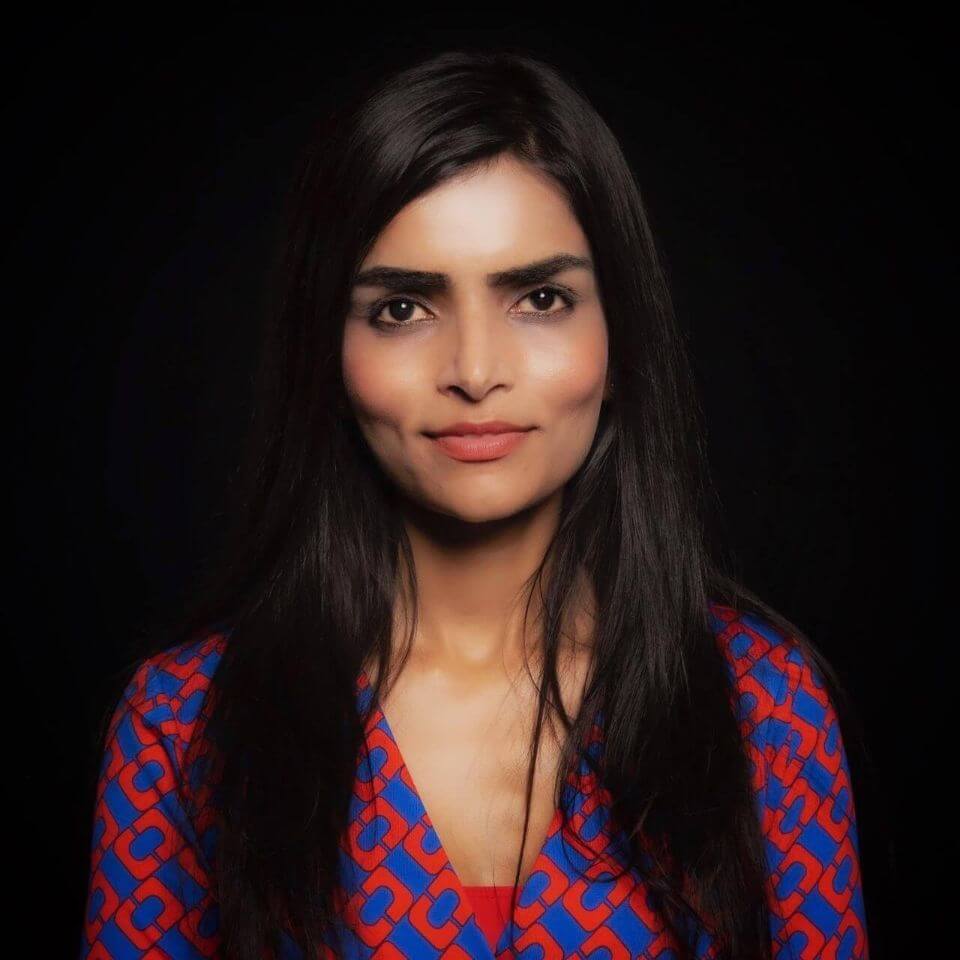
Suuchi Ramesh founded Suuchi Inc. 4 years ago after a 12 year career in technology and predictive data analytics. Before starting Suuchi Inc., Suuchi had scaled the B2B side of multiple tech startups from zero to nearly $30 million. Suuchi now plans to do the same with the GRID. The Suuchi GRID is an intuitive software solution that digitizes the entire supply chain, empowering participation, and providing a single source of truth across suppliers, factories, brands, retailers, warehouses, and customers.
Learn more about Suuchi Ramesh
Learn more about the GRID