What is Supply Chain Collaboration?
Supply chain collaboration has been a hot topic for many years, with McKinsey highlighting the importance back in 2012 for retail and CPG businesses specifically. Nearly a decade later, many companies have yet to actively implement strategies and tools to support end-to-end collaboration across their supply chains. In the past, it was possible to credit increased collaboration through increased strategy sessions across teams that influenced the value chain and more frequent in-person visits to suppliers. However, the current supply chain landscape requires a digital solution to support collaboration initiatives.
Supply chain collaboration is when two or more organizations plan, work, and execute on supply chain operations. These organizations will include internal teams, factories, raw material vendors, warehousing facilities, and distribution centers for most global supply chains.
Who is Involved in Supply Chain Collaboration?
Supply chain collaboration includes all value chain participants including, but not limited to, freelancers, designers, supply chain managers, sourcing agents, factory workers, logistics partners, and top-level executives. Since the supply chain impacts every facet of a business, it is imperative to consider how all of these participants will use a new collaboration tool.
Where is Supply Chain Collaboration Going Next?
As we move into the next generation of supply chains, collaboration that extends past internal partners is the key to success. Incorporating vendors, suppliers, and downstream partners when implementing a new software will differentiate companies that scale to new heights from companies that remain stagnant. When all participants have a seat at the digital table, decision-makers ensure data integrity and see how team members leverage data to make critical decisions.
What is Supply Chain Partnering?
Supply chain partnering is when two or more companies collaborate to extend their existing capabilities. For example, a PLM provider may form a partnership with an ERP solution to expand their offerings and capabilities for their potential and current customers. While these partnerships provide benefits for the solution providers, it does not address the need for collaboration across the participants using those systems leading to siloed data and miscommunication that can cause costly delays or errors.
Why is Supply Chain Collaboration Important?
If there is broken or minimal collaboration across the supply chain, operations will not run efficiently, ultimately impacting margins, timelines, and overall customer satisfaction. However, once an effective collaboration tool is put in place, businesses can quickly see their margins increase by up to 15% and turnaround times decrease by up to 50%. A digital collaboration solution also helps companies improve their supply chain by taking previously on-premise functions and turning them into streamlined software features.
How to Avoid Supply Chain Collaboration Mistakes
While the benefits of increased collaboration are exciting, there are certainly pitfalls if a new solution is implemented incorrectly. At Suuchi, we work with hundreds of companies to outline an effective digital collaboration strategy. Below are the tips we share with our customers who are ready for improved supply chain collaboration:
- Identify the right solution: The communication platform industry is currently valued at over $4B and is only expected to grow given the increased dependence on tools like Zoom and Slack. However, most of these platforms are not built to address supply chain participants’ needs, from internal operations managers and executives to factory managers and logistics coordinators. When most of these platforms are not inclusive for half of your value chain participants, it is essential to vet software vendors to ensure that it is intuitive for all users.
- Start at the top: Whether you are part of senior leadership or proposing a new solution to your higherups, it is vital that the entire leadership sees the value in a new system. Most collaboration tools are siloed by departments or were not designed for users of diverse skillsets. When proposing a new solution, be sure to outline the value for all organizations to improve the entire value chain, not just a few people across the organization.
- Onboard key users first: If you try to onboard all of your internal and external users at once, it will be very difficult to get the buy-in for participants to see the value of changing their current way of doing things. Instead, start by onboarding internal “champions” of the system that will use it the most. Ensure they feel comfortable with the system and become internal experts on all the relevant features. Once they are up and running, you can allow them to train additional internal users to increase the internal buy-in and engagement before opening up the system to outside participants (i.e., freelancers, vendors, and logistics partners) who might require more convincing.
While implementation and onboarding will vary based on the chosen solution, these three tips help simplify the process across the board.
What is the Difference Between Supply Chain Collaboration and Supply Chain Coordination?
Supply chain coordination improves supply chain processes by aligning the different entities’ goals and plans across the value chain. Supply chain collaboration supports coordination by enabling a supply chain coordinator to have real-time access to all of the different players across the supply chain and simplifying how they access the data needed to make critical decisions. Suppose the communication and collaboration process breaks down at any point. In that case, supply chain coordination becomes much more complicated. It will lead to managers making decisions on false data, which can cause delays, reduction in margins, and faulty finished goods.
Integration with Existing Collaboration Tools
Anytime a company is considering a new software investment, they need to understand what already exists within their tech stack. Particularly with collaboration tools like email, text, and WhatsApp, internal and external partners might feel more comfortable using those same platforms instead of introducing another system. As mentioned earlier, the solution must have the critical features needed to accommodate all users. That makes open APIs and SDKs imperative to allow for these key integrations for communication. For example, if a text is sent on WhatsApp or a user responds to a notification through email, there should be integrations to track those responses and pull them into the system. This integration eliminates some of the onboarding friction and creates a single source of truth for all communication.
Conclusion
Beyond internal teams, supply chain collaboration is imperative for supply chains to thrive and scale for years to come. While there are hundreds, if not thousands, of options on the market, innovation leaders need to identify the solutions built with all types of supply chain users in mind. Once the right solution is in place, companies will enjoy the benefit of improved operations leading to increased margins and improved turnaround times.
The Suuchi GRID’s Communication and Collaboration module works in conjunction with the entire product suite to enable a simplified collaboration process for all participants. Users can access features like native chat, file- and project-level comments, video conferencing, and real-time updates from internal and external stakeholders from the web or the mobile app. Our customers see up to a 15% improvement in COGS and up to a 50% improvement in turnaround times through streamlined collaboration across the value chain.
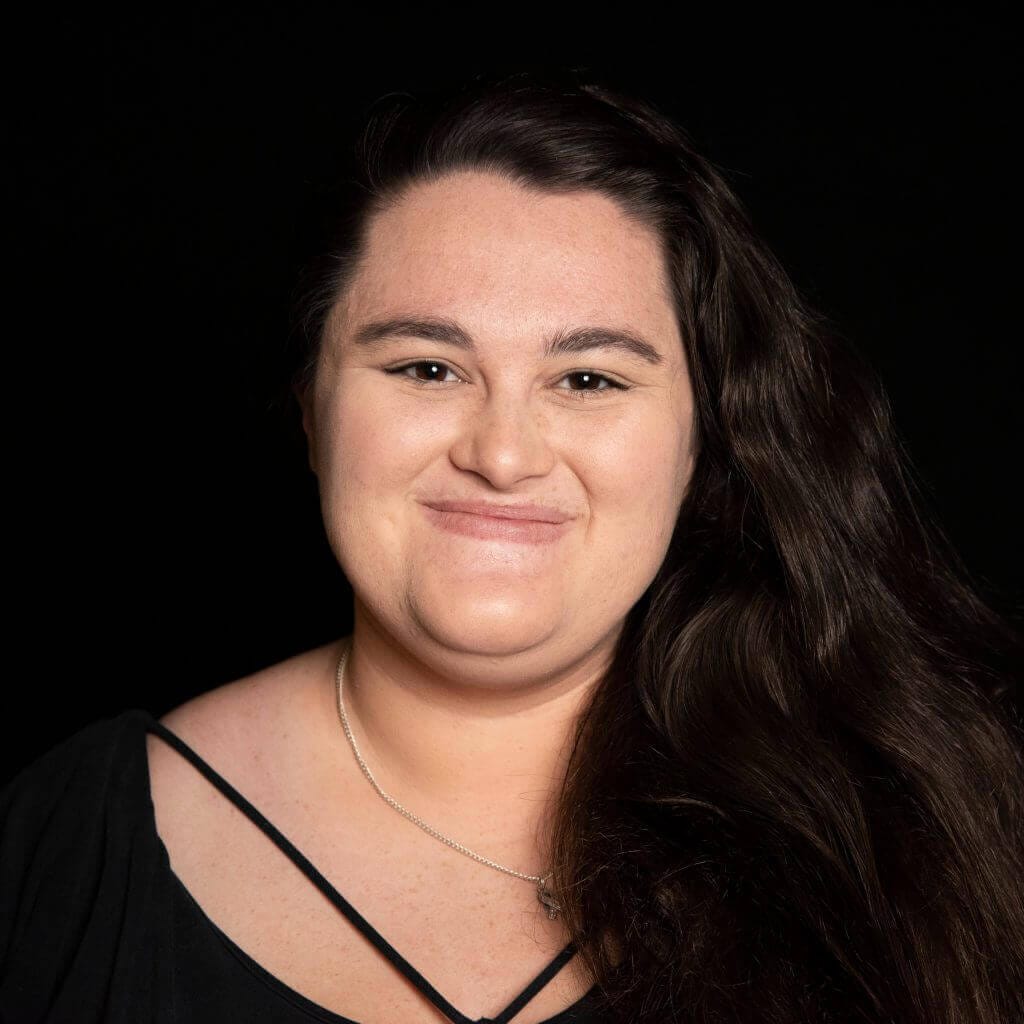
Lizzie Sessa is the Senior Manager of Product & Content Marketing at Suuchi Inc. She works with the Sales and Product teams to support go-to-market initiatives and promote the need for supply chain digitization. Learn more about Lizzie.