Described as the most significant step towards the Industrial Internet of Things by various industry insiders, digital transformation could be ripe for adoption. Complementing industries like fast-moving apparel businesses, the digitalization of manufacturing has been transforming operations, processes, and energy footprint of factories and supply chains. Giving more than just a quick boost to productivity, the digitalization of production has been, transforming the traditional fashion supply chain to digital supply chains, by improving how products are designed, fabricated, used, and serviced.
Adidas recently announced its intention to move its Speedfactory technology to Asia by April 2020. After investing heavily in digital supply chains, the footwear giant has made a strategic move that has meant that production will be discontinued at their Ansbach and Atlanta Speedfactories within the next six months. The company seems to have decided to take a few steps back from the “future of manufacturing to America” and bringing it back to Asia. It is a decision that has had many industry commentators wondering whether Adidas’ SpeedFactory still has the oomph to supersede conventional production.
Driven By Innovation and Disruption
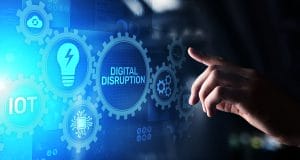
To understand whether Adidas’ SpeedFactory could have had the clout to outmode conventional production in Asia, you have first to understand what a SpeedFactory is and what it brings to the table. Adidas defines it as a smart manufacturing process via robotic automation that integrates the design and production process tailored to a specific market. Developed to bring production closer, hence why they set camp in the US, Adidas’ Speedfactory was also a representation of what variations of Speedfactory footwear models could operate like in the future.
It was back in 2016 (Ansbach) that Adidas acquainted us with the first pair of Speedfactory sneakers- a limited-edition running shoe called Futurecraft M.F.G (Made For Germany). It was an introduction that was accompanied by a 3-minute teaser video that highlighted the manufacturing process of the speedfactory. On the release of the 500 pairs, Gerd Manz, vice president of Adidas’ innovation group, stated: “What we enable is speed. We can react to consumer needs within days.” In 2017 they opened another Speedfactory in Atlanta, GA, USA.
Intended to be the factory that reinvents the industry, Adidas Speedfactories was designed to change the existing manufacturing model, which is producing the Adidas product in eastern Asia and then shipping it to where it needs to be. By changing direction, Adidas’ Speedfactory was able to reduce the time from design to finished goods from 12 to 18 months to as little as 45 days. It was a change that is perfect for the fast-moving fashion or sports industry. Using the new production methods developed in Ansbach and Atlanta, Adidas’ re-designed process concentrated on the supply chain in one location, modernizing its other suppliers and applying 4D technology in footwear production.
The Early Adoption of High-tech Manufacturing
With pressure on retailers to increase their speed to market, Speedfactory technology was intended to transform Adidas’ supply chain in a way that would help them continue to be a provider of over 900 million sports and sports lifestyle products. So why did they close their high-tech manufacturing factories? My initial thought was whether Adidas committed to a technology that wasn’t ready yet. It was thought that based on the fact that digitalization is still considered to be in its early stages, so when Adidas implemented the technology into their whole organization, it raised specific challenges like building momentum and scale.
On their sudden shift away from the Speedfactory Adidas global operations head, Martin Shankland explained in an official press release that the Speedfactories had been instrumental in furthering their manufacturing innovation and capabilities, which was their goal from the start. Adding: “The knowledge we gained from setting up and operating the Speedfactories was made possible through constructive cooperation with OECHSLER and the team there. With this, we have pioneered new manufacturing processes, including a significant reduction in the production time of athletic footwear. We very much regret that our collaboration in Ansbach and Atlanta has come to an end and thank all project participants for their commitment. At the same time, we are pleased to continue our partnership with OECHSLER in other areas, especially in advanced 4D printing,”
Dr. Claudius M. Kozlik, CEO of OECHSLER AG, also commented in the press release: “Whilst we understand Adidas’ reasons for discontinuing Speedfactory production at OECHSLER, we regret this decision. At the same time, we look forward to continuing our close and trusting cooperation with Adidas in the area of 4D sole printing. With the Speedfactory production for Adidas, we have gained important insights that have already been and will continue being incorporated into the production of other OECHSLER Group divisions – Automotive, Medical, and Innovative Solutions.”
Led by innovation, Adidas foresaw a future where all their product categories will be produced using the production processes tested in the Speedfactories. Changing direction, the multifaceted organization has stated that going forward; their SpeedFactory will now act as a separate business model that will complement their Asia operations rather than replace them. With plans to continue establishing strategic partnerships, the sports brand’s Speedfactory has started a conversation on how industries can revolutionize their supply chain. As Adidas continues to lead in the innovation field, I can report that the company plans to continue to transform its traditional practices into digital supply chains for its organization, using technology. Doing so will undoubtedly help them escape their current manufacturing trap, which we all know is outdated and very much in need of innovation.
Learn more about how to implement a data-driven supply chain